Milling and drilling are two of the most commonly used machining processes. To the inexperienced, these two processes might seem the same. However, to those who have enough background and practice, it’s easy to spot their differences. Essentially, both processes remove materials from a workpiece.
With the help of these two processes, machinists can manufacture pieces according to certain specifications. Understanding the key differences between these two is essential to manufacturing metal, wood, and other types of workpieces.
What is CNC Milling?
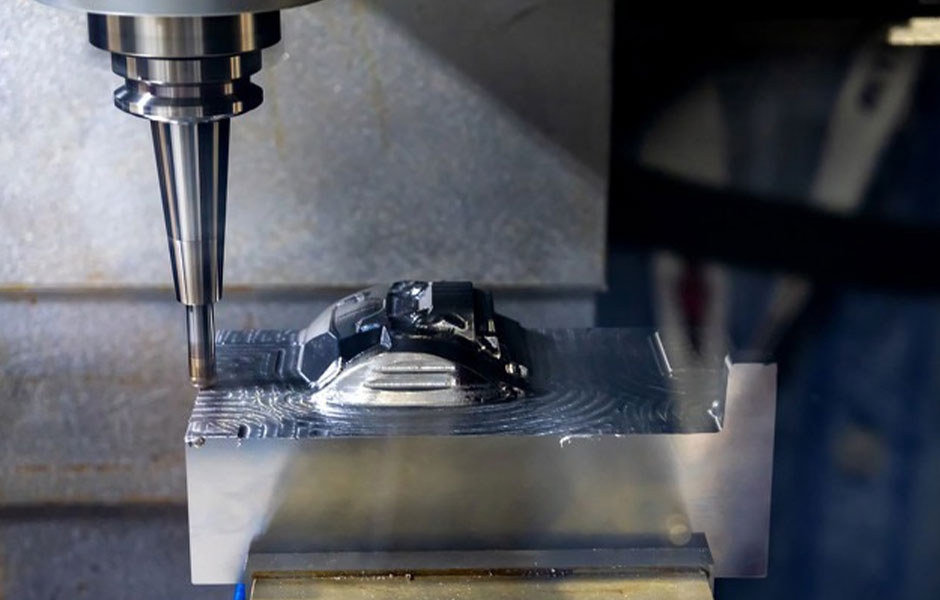
When it comes to CNC Milling, the process is a subtractive one, that uses the computer numerical control system for automation, and crafts by taking materials away until the finalized and finished designs are formulated.
Milling is the term used for the process of cutting and drilling materials (often wood, plastic or metal), and generally utilizes a rotating cylindrical tool (a milling cutter) that is held in a spindle. These can range in form and size and offers the ability to move along a different axis to cut at different angles to create slots, holes, and details in the material.
Before CNC technology, milling machines came in a variety of types (ranging individually from 2-axis to 5-axis machines) with each progressive numerical value adding a different axis or function. Since CNC Milling machines are computer operated, they make use of any number of axes (from 2 to 5) and don’t require manual operation.
Modern CNC Milling machines can be assembled as both horizontal and vertical machining centers – a vertical machine has the axis orientated in a vertical position, and usually has long thin cutting tools – these are generally cheaper than horizontal mills (prices can be up to 4-5x different) and are more often seen in workshops (because of the availability afforded by the lower price), and are considered easier to use (with increased user visibility of the work zone).
Horizontal machines are orientated with the axis in a horizontal position and generally have shorter and thicker cutting tools. When comparing the two, horizontal machines are considered to be less versatile, but also much better suited for long material work, as they also allow for parts to be created with fewer operations, a better surface finish, and faster milling.
Because of the huge range of designs that can be created with a CNC machine, it’s no surprise to find that there’s a range of different types of CNC Milling machines available, varying in size to better suit the jobs they’re used for – such as Turret Mills, which work vertically with a fixed spindle (the table adjusts to do the job), which are best suited for detail work, or Bed Mills which are built on larger more rigid frames and are often utilized for mid-sized production that the Turret would be too small to handle.
Choosing the right machine for the job is an important decision, as the different sizes, functions, and operating capabilities play a huge role in whether or not it’s fit for purpose.
The milling process has several different steps that see it through from start to finish – designing the required part in CAD (Computer-Aided Design), translating that file into machine code, setting up the machinery, and allowing it to create the part.
Care has to be taken, especially in the initial stage, to ensure the model that’s being designed is possible to produce, and that the machine is set up properly to handle it.
Some of the benefits and features of CNC milling are as below:
- It is ideal for rapid prototyping and mass production.
- It requires less lead time and thousands of milling parts can be produced in a short period of time.
- It produces parts with extreme precision and accuracy.
- Automation reduces labor and manufacturing costs.
- Its multi-axis operations help in developing parts with complex geometries.
- It comes with high operational reliability, good adaptability, and flexibility.
Uses of CNC Milling
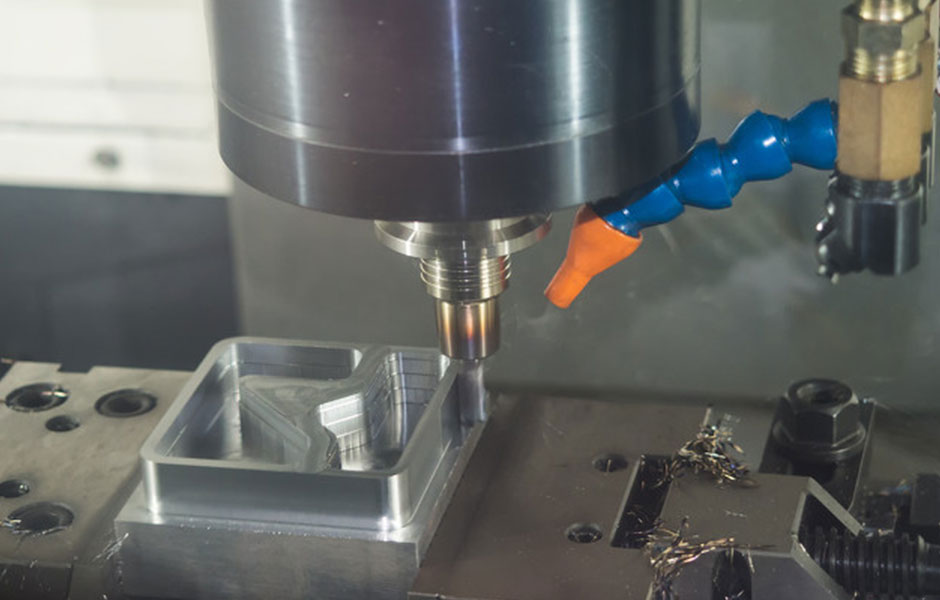
CNC Milling machines, with their versatile cutting abilities, and superior precision, are used in many different industries, and for a range of different parts or products.
There is a wide assortment of cutting tools available for most machines, and these allow for greater flexibility, and opportunities to work with different materials, which further increases the usability of CNC Milling in different lines of work.
The four main types of milling cover:
Plain Milling
-Also known as slab or surface milling, this is used for creating a flat surface
Face Milling
-The rotary axis is set perpendicular to the material’s surface and combined with tooth-cut tools, to cut raw materials, with those in contact with the flat material being used for finishing.
Angular Milling
-As you might expect from the name, this involves the tool’s axis being set at an angle from the raw material’s surface, and this provides a midpoint between Plain and Face milling.
Form Milling
-This is the milling used for creating parts that have no flat surfaces, and the machines involved are often fitted with multiple different tools during the task, to obtain the curves or shapes desired.
Because of the versatility, the CNC Milling process brings (you’re pretty much only limited by the workability of the design), the techniques are used for a huge number of projects. They are perhaps most commonly associated with the automobile and aerospace industries (creating car and plane parts respectively), but due to their compatibility with a variety of materials (such as steel, aluminum, copper, titanium, bronze, wood, nylon, extruded polyurethane, stone, and plastic), the process is also used for projects such as:
- Sculpture
- Prototype and Modelling
- Woodworking
- Instruments
- Aluminum Machining
- Plastic Machining
- Furniture
- Signage
- Cabinet and Shelving
Depending on the project, the usage (whether it’s from a hobbyist or an industrial complex), and the scale of the project, there is a huge range of uses that CNC Milling machines can bring with them.
What is CNC Drilling?
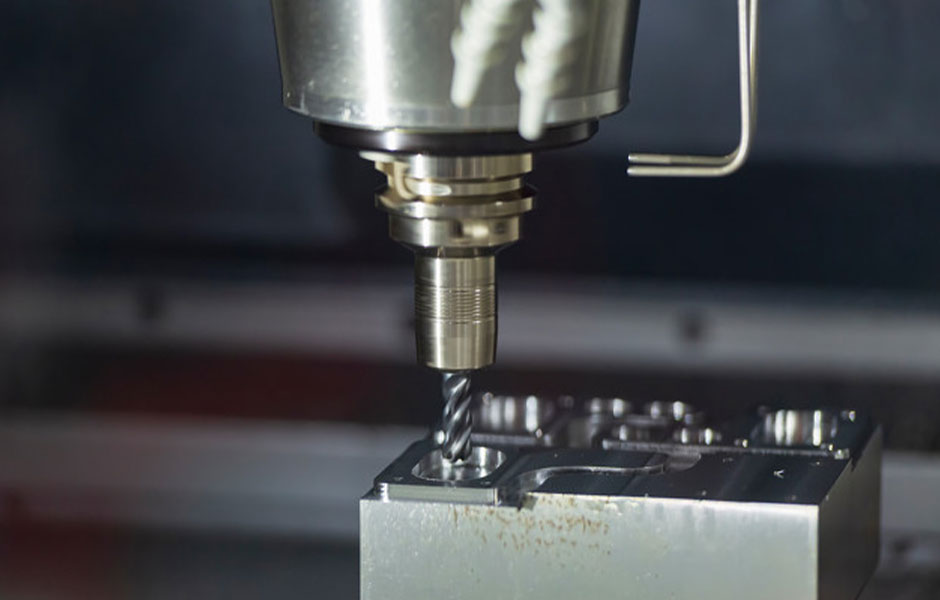
Unlike CNC Milling, which utilizes multiple axis and movements to form a product or part, CNC drilling is a process that utilizes a rotating cutting tool, which produces round holes, this is done in a stationary workpiece and is commonly implemented for mass production as it makes for a more efficient production line.
Similar to the CNC Milling machine, these machines use computer code to automate the drilling process as they work in tandem with CNC software which sees a design created in CAD formatted into code and inputted into the machine, where it follows the instructions to drill with increased accuracy and efficiency compared to traditional methods.
Whilst CNC Drilling machines are more commonly found in industrial settings, a wider range of cheaper machines is becoming available, and is opening up their usage to hobbyists and smaller businesses.
These machines are capable of working with different materials, such as glass, wood, plastics, and soft metals. They come in a range of sizes and styles, including upright, bench, and radial – and there are multiple elements in each machine such as the spindle (for securing the chuck and drill bit), the table (to provide the workspace for the drilling machine), a column (for supporting the CNC machine elements), drill bit (for the actual work), and interface (for controlling machines with operator input).
There are a variety of factors to consider when looking at a CNC Drilling machine, including the size of the working area available, its compatibility with the projects at hand, durability, torque level, spindle speed, and usability.
Once a machine is set up, the usability phases go from the operator uploading the CAD or CAM (Computer-Aided Manufacturing) design to be converted to code, installing the correct drill bit, securing the raw material to the table, starting the drilling process through the interface, and letting the machine get to work drilling holes of appropriate sizes and diameters.
Some of the benefits and features of CNC drilling are as below:
- It is extensively used in manufacturing high-quality molds.
- It can easily drill a hole up to a depth of 2600 mm and a diameter of 3 – 32 mm.
- It is capable to drill complex machine parts according to your need.
- It requires less lead time as compared to manual drilling.
- It is a computerized numerically controlled machine, that produces premium parts with extreme precision.
Uses of CNC Drilling
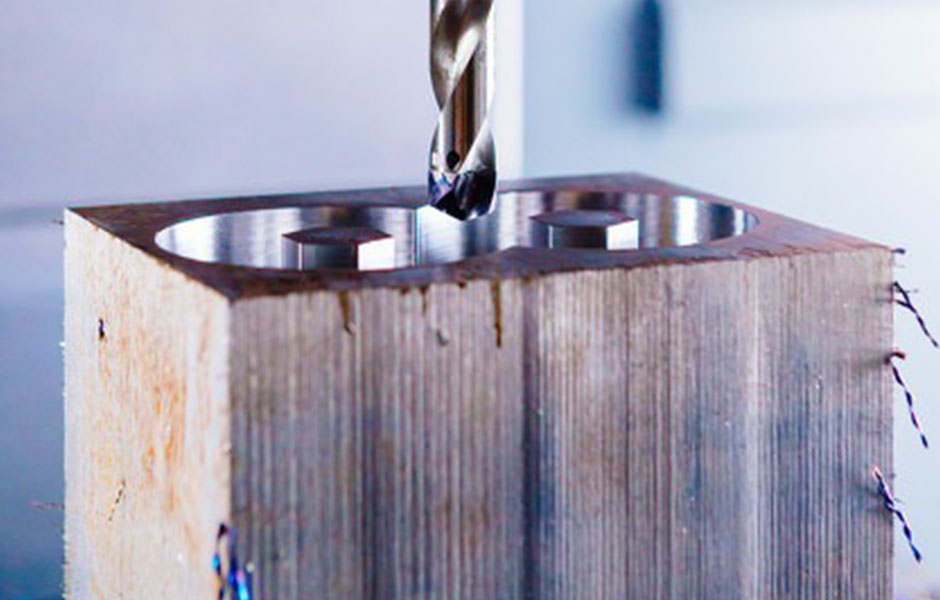
For projects that require a higher degree of accuracy, broader versatility, and greater reproducibility, CNC Drilling machines are a smart option – because they work to design, there is no human error involved with the process, the machines will create parts that replicate the CAD / CAM design, which allows for high consistency to be achieved through and between batches – this has led to CNC Drilling being a popular option for creating parts such as hubs, machine shafts, gear blanks, aluminum or plastic profiles, and more.
Drilling Machines with CNC are mainly used for reaming, chamfering, and drilling – and are largely used by automobile, aeronautics, astronautics, shipbuilding, and engineering industries for complex parts.
Common applications of these machines include:
Metal Fabrication
-Precision holes are drilled into solid metal materials to create precision parts. These techniques are often found in automobile, aerospace, and construction industry projects to produce end parts.
Wood Fabrication
-The CNC machine is part of standard operations for wood manufacturers (such as furniture makers, cabinet makers, etc). The Drilling Machine is often used in conjunction with other CNC machines to provide standardized levels of turning, milling, and grinding.
Components and Parts manufacture
-It’s common for manufacturers to use a CNC machine for drilling, especially in industries where precision and repeatability aren’t just a nice thing to have, but critical to the success of the products (such as computing).
Plastics Manufacturing
-Because of their versatility, and ability to work with different styles and tools to create standardized products, manufacturers of different plastics also utilize CNC Drilling to fabricate electronic parts.
Electrical Applications
-CNC Drilling (and other CNC machines) are essential for businesses in the Electrical Industry. With Drilling Machine manufacturers have been known to use them as electrical discharge machines in several instances.
The type and size of the machine, the tool or bit used, and the complexity of the job all play a role in what drilling machine works best for the job at hand, but with interchangeable parts, and the ability to create fine precision pieces with reliable repetition, the CNC Drilling machine is certainly a valuable tool in many businesses’ workshops.
Conclusion
We found that CNC milling is a bit complex and a lot of machining processes can be performed on this single machine. On the other hand, CNC drilling is limited in its operations and is typically used to drill holes in the workpiece. Both of the processes are used to produce high-quality parts that meet the requirements of every specific individual.
CNC MACHINING SERVICE
DFM China is a CNC manufacturing and sheet metal fabrication company, including CNC machining services, CNC milling services, CNC turning services, laser cutting services, and stamping services.
DFM China offers professional CNC machining and rapid prototyping service for making a wide array of product parts. Our excellent quality control systems ensure that all our deliveries are speedy and standard for every manufacturing size in both low-volume and high-volume productions. Feel free to reach out for a free quote on your project.