CNC machining is a versatile and cost-effective manufacturing process. This process is compatible with a huge range of materials. As such, CNC machining helps across a diverse array of industries for a variety of applications. Manufacturers and machinists use this process in various ways. This includes direct manufacturing process, indirect manufacturing process, or in conjunction with other processes.
CNC machining is considered a subtractive manufacturing technology, which means that the end product is formed by selectively removing excess material from the workpiece. Every end-to-end CNC machining operation follows a similar four-step production process.
These four production phases are:
Part Design
Parts produced via CNC machining generally start out as initial designs from Computer Aided Design (CAD) software. In the design phase, engineers give careful thought to all aspects of the desired final product, such as parameters for optimal performance, operating conditions for the end part, and acceptable tolerance variation levels.
Design Conversion
Upon completion of the initial design phase, the CAD model must be converted into a functional CNC program using Computer Aided Manufacturing (CAM) software. CAM software is able to extract the geometrical requirements from the CAD model’s origin file and translate them into a CNC-compatible programming language—such as G-code or M-code—which will dictate the mechanical operations of the machine.
CNC Machine Preparation
Next, the CNC machine operator must set up both the machine and the target material according to the specifications required by the CNC program. The operator will ensure that the correct cutting or drilling tools are properly installed and are matched with the appropriate bits or end mills. The operator must also set up the workpiece, typically either in a stationary clamp or attached directly to the CNC machine.
Executing Programmed Operations
Finally, the CNC machine operator executes the desired mechanical processes. During operation, the CNC program precisely controls the movements of the machine tooling.
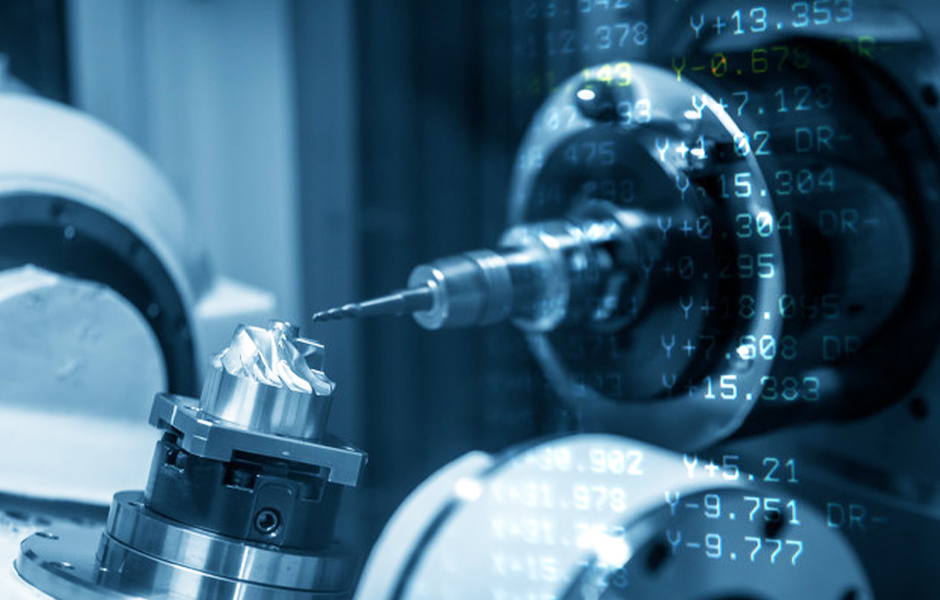
Applications of CNC Machining:
CNC machining is a manufacturing process used in a variety of industries, including automotive, aerospace, construction, and agriculture.
CNC machining processes are suitable for a variety of engineering materials, including metals (such as aluminum, brass, stainless steel, alloy steel, etc.), plastics (such as PEEK, PTFE, nylon, etc.), wood, foam, composite materials, etc.
Advantages of CNC Machining and Products:
- The automated nature of CNC machining enables the production of high-accuracy, high-precision, simple parts, and cost-effectiveness when completing one-off and medium-volume production runs.
- High precision and high quality.
- Data is easy to store and modify. If the programming is good, the machine tool can be used at different times and places to produce the same product. No redesign is required.
- It can automatically change tools, feed materials, etc., with a higher degree of automation.
- Adaptive control maintains the machine tool in optimum production conditions.
- Longer tool life.
- Can perform calibration of complex product specifications and shape requirements
- Products that can be mass-produced
As with any manufacturing process, the unique advantages of CNC machining inform the kind of applications for which it can be used. However, the benefits of CNC are desirable in virtually any industry. They are suitable for many parts and products. Since CNC machines can process almost any type of material, their applications are near limitless.
CNC Machining Service
At Dfm China, with a lineup of advanced CNC machining equipment and a commitment to precision, we can handle machining projects ranging from prototype orders to high-volume production runs. Request a quote to start your order.